PCB Assembly
aka PCB population
Eastwin Service: PCB Manufacturing + Assembly Since 2001
Shenzhen Eastwin Ltd. has provided full or partial turnkey PCB manufacturing & assembly service since the year 2001, ranging from PCB board fabrication, components sourcing, PCB assembly(Also known as PCA or PCBA) service to functional testing & products assembly. We always produce customers’ products based on our ISO Certificate standard. Now we have 8 SMT Line and 3 DIP line.
EASTWIN aims at superior quality, perfect service, creating extraordinary value, Being a first-class enterprise, to reach our goal – provide our customers with better and better service.
Main Production and Inspection equipment (8 SMT LINE 3DIP LINE)
ITEM | Device Name | Model | Manufacturer | Qty | Remarks |
1 | Full Automatic Screen Printer | DSP-1008 | DESEN | 8 | |
2 | SMT Machine | YG200 | YAMAHA | 5 | 8 SMT Line |
3 | SMT Machine | YV100XG | YAMAHA | 3 | |
4 | SMT Machine | YG100XGP | YAMAHA | 19 | |
5 | SMT Machine | YV88 | YAMAHA | 5 | |
6 | Reflow Soldering | 8820SM | NOUSSTAR | 4 | |
7 | Reflow Soldering | XPM820 | Vitronics Soltec | 3 | |
8 | Reflow Soldering | NS-800 II | JT | 1 | |
9 | Solder Paste Inspection | REAL-Z5000 | REAL | 1 | |
10 | Automatic Optical Inspection System | B486 | VCTA | 3 | |
11 | Automatic Optical Inspection System | HV-736 | HEXI | 5 | |
12 | X-Ray | AX8200 | UNICOMP | 1 | |
13 | BGA Re-work | MS8000-S | MSC | 1 | |
14 | Universal 4*48-pindrive concurrent multiprogramming system | Beehive204 | ELNEC | 3 | |
15 | Automatic Plug-In machines | XG-3000 | SCIENCGO | 2 | |
16 | Automatic wave soldering system | WS-450 | JT | 1 | 3 DIP LINE |
17 | Automatic wave soldering system | MS-450 | JT | 2 |
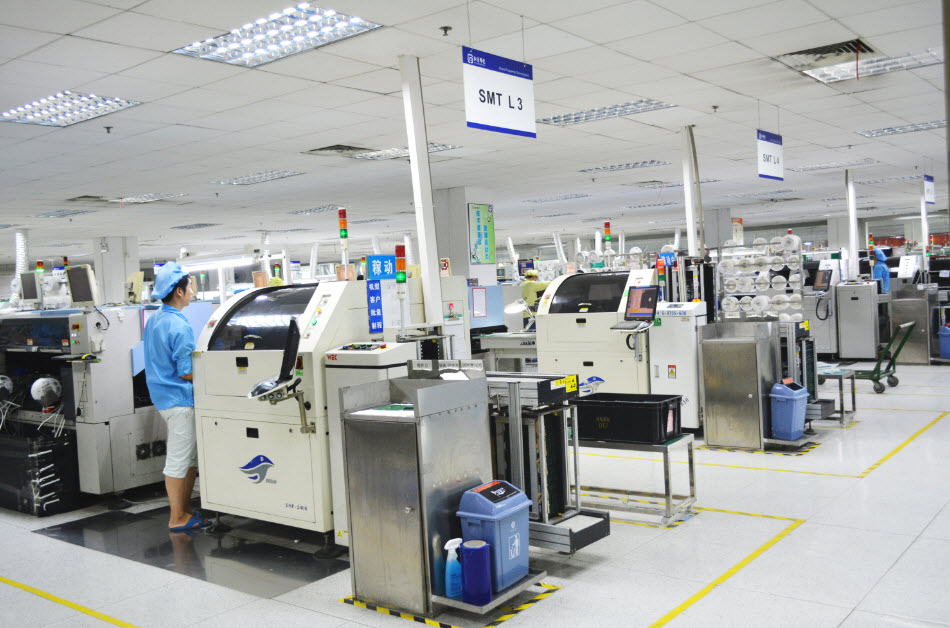
8 SMT Line
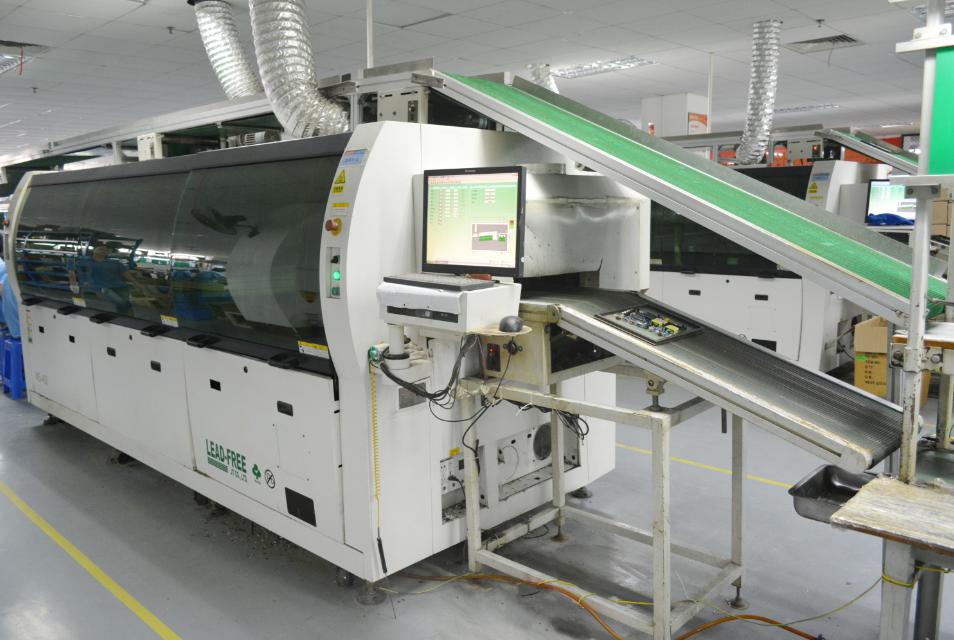
Reflow Soldering
PCB Processing Capacity
SMT production capacity 10 million chip per day(for 0402, 0201 components up to 8 million per day), DIP production capacity is 1.2 million pcs per day.
We can also provide firmware loading, conformal coating, plastic inject, cables and plastic assembly based on customers’ requirements.
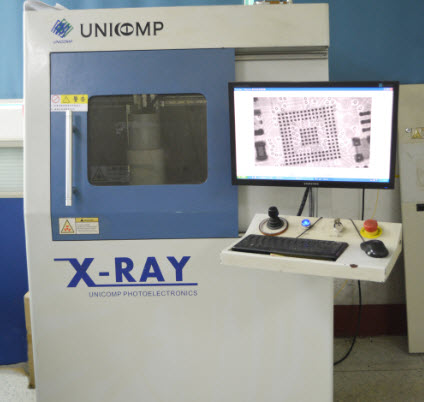
BGA chips assembly & checking
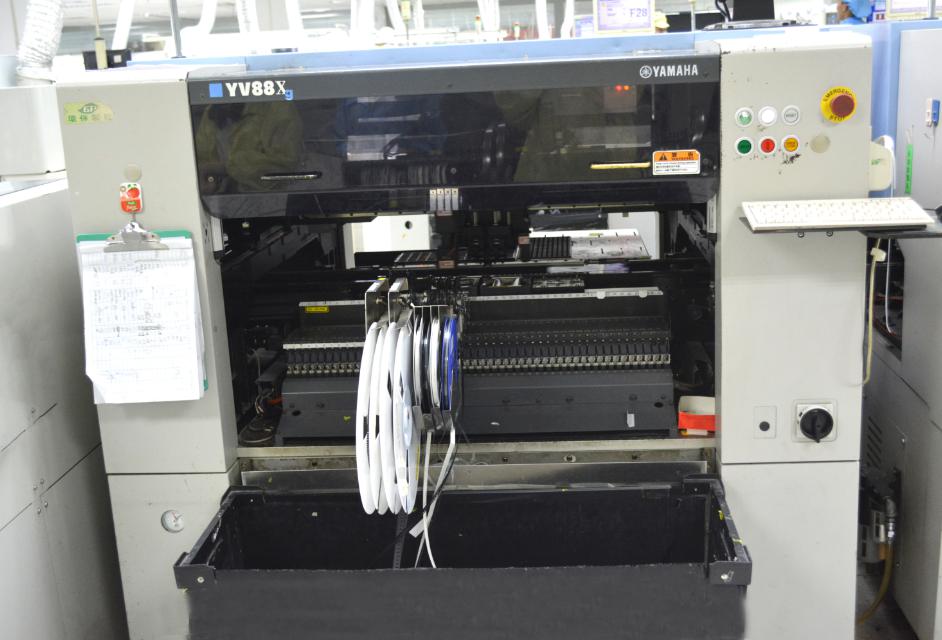
SMT production capacity
Quality Assurance
- 100% AOI Inspection
- 100% Product Functional Testing for Free
- 2-year Quality Assurance
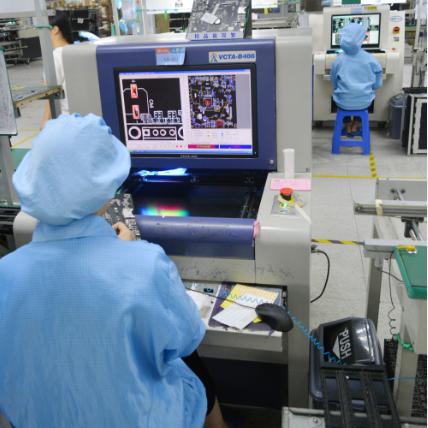
Full AOI Inspection
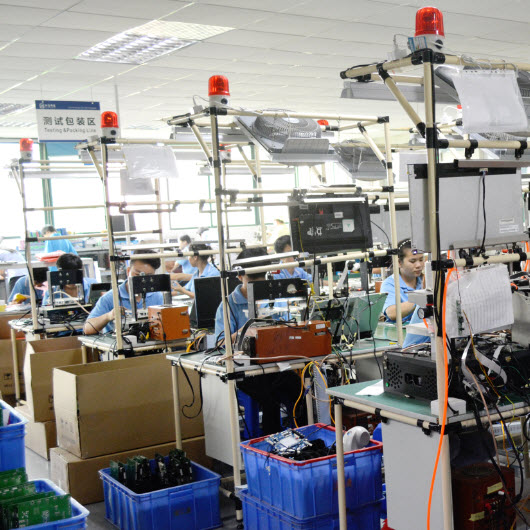
Functional Testing
PCB Assembly Testing
PCBA testing is a very important procedure to make sure PCB Assembly quality after assembly. Before out of our factory, every piece of board needs strict testing, and in general, Eastwin PCB Tests include the following 4 procedures:
1. Visual inspection after SMD Process
Each SMT lines have one QC person to check the SMD solder quality after assembly.This step is visual inspection, here to verify if any parts loss or incorrect parts are used via checking the BOM list. After finished the visual inspection, then move to second test- AOI testing.
2. AOI Testing(X-ray Testing for BGA package)
After the first step of checking components with pads, we start to assemble SMD parts.
And will do AOI testing after all the SMD parts finish. AOI test means Automatic Optic Inspection, it is used mostly in Assembly industry, and it can test many defects:
- Components offset
- Components polarity error
- Less solder paste
- No solder paste
- Cold solder
- Soldering Joints
For BGA package component, we additionally do X-ray test.
Now more and more companies use BGA package(Ball Grid Array package) ICs for their design, but BGA raises the higher requirement to soldering, so the test after assembly is very important, X-ray is a professional machine to check the inner solder problem of BGA.
3. Free Function Testing with test jig
If above testing is passed, then the next step is functional test. For 100% make sure the quality, we do functional test for customers free of charge, provide free testing jig and free program burning.The testing method is usually offered by customers; but if customers couldn’t provide it, our engineer will design a test method for the board as well.
4. Final visual inspection
The last step is visual inspection in QC department before cleaning board, we use a magnifier to check the soldering and direction of components.